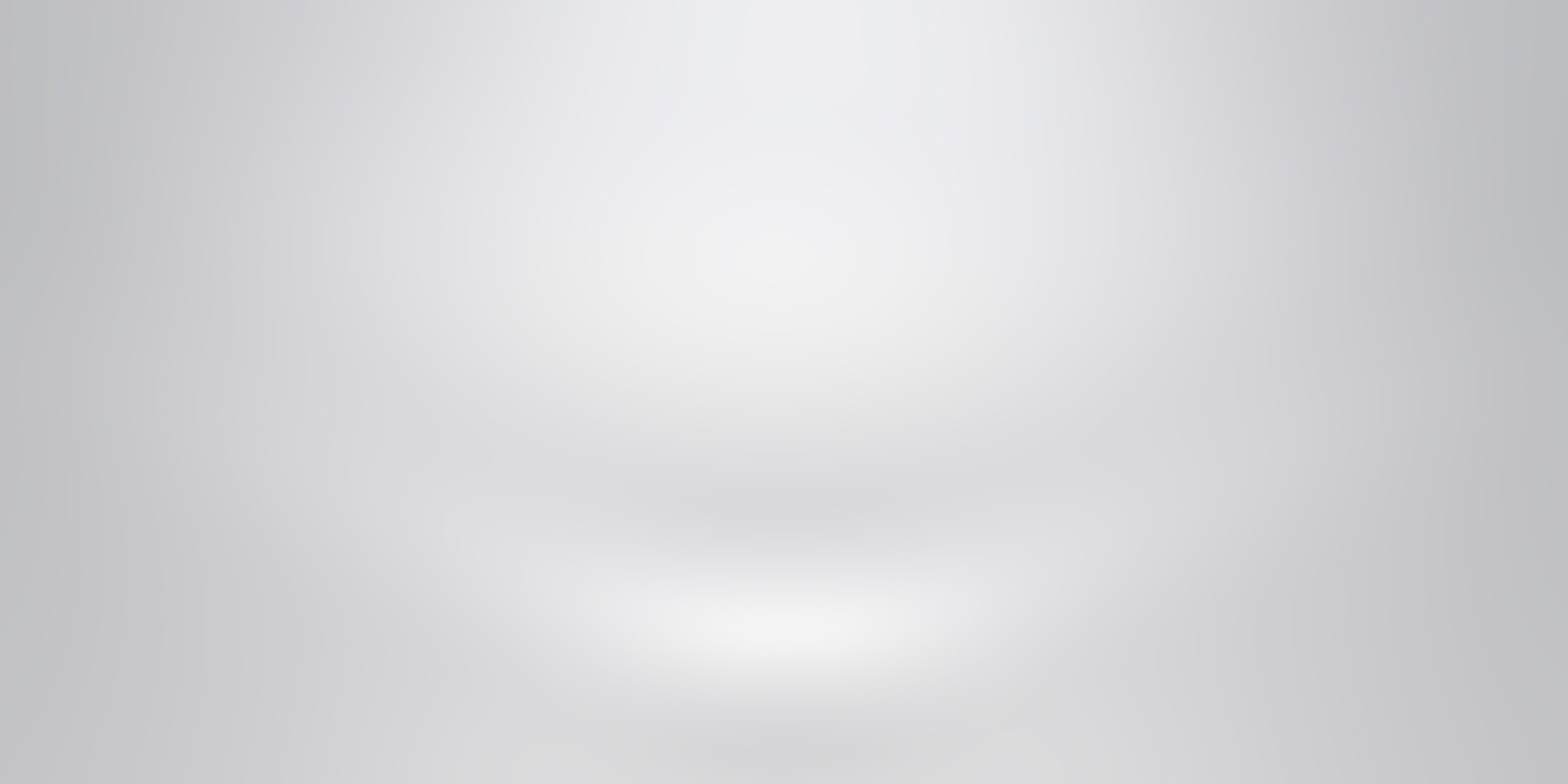
Technology
Our Technology Sets Us Apart
Many plating companies advertise automated plating lines - but not all automation is created equal. Keep reading to learn a bit more about our technology and how it allows Varland Plating to deliver industry leading quality, consistency, and turnaround performance for our customers. Let us show you how our commitment to in-house expertise in both plating and technology has allowed us to develop custom and innovative solutions that we believe are unmatched in the plating industry.
Technology is in our DNA
Long before we were designing automation systems for our plating lines, Varland Plating developed our own custom software for running our business. Our in-house programmers began writing COBOL programs for an IBM AS400 server in the early 1980’s and we haven’t looked back since. We even marketed and sold our software to other plating companies. Many of the core components of this software remain in use and still provide us with a competitive advantage due to being speciifically designed for our needs as a barrel plater.
In an industry that hasn’t always been known for being on the leading edge of technology, our founders’ early embrace of technology is still paying dividends today. When we need a new integration between our existing production control system and a new piece of equipment used on the plant floor, we can make that a reality because of the foundation laid decades ago to promote and maintain strong in-house technological and programming capabilities.
Throughout the ‘90s and ‘00s, Varland sold our business software to other plating shops and provided phone support
Anatomy of a Varland Automated Plating Line
At Varland, the automation actually begins before customer parts make it to one of our plating lines. When an order of customer parts is received, it is immediately entered into our proprietary production control system and is identified with an in-house order number. Our system then tracks each customer order through our entire process from receipt through shipment assuring lot integrity. Our software maintains a database of all the thousands of different parts we plate. This database includes part-specific information, including a detailed plating procedure/recipe. Plating procedures are built from a series of standardized instruction codes along with part-specific instructions tailored exactly for each part. This system allows for control and consistency within certain similar groups of parts and/or from order to order of the same part. Historical data (shipment history, process/procedure history, etc.) is also maintained for each part.
The fun really begins when the custom plating recipe is downloaded to a PLC (programmable logic controller) controlling an automated line. Our PLCs are programmed to monitor and control nearly every aspect of our automated lines. PLC automation starts before customer parts are even loaded into a plating barrel - the system monitors a load scale and verifies that the right size load is loaded into the barrel per the plating recipe. The system will also adjust specific plating parameters based on load size variances. All plating barrels are outfitted with RFID tags that are read by readers on the hoists. Every time a hoist moves a barrel, the PLC knows exactly which parts are in the barrel allowing monitoring and control of plating process parameters - barrel rotation, tank temperature, rectifier voltage/amperage, etc. Even after parts are unloaded from a plating line, our PLC’s monitor the drying process.
A failure at any stage of the plating process can lead to quality problems and/or missed delivery deadlines. We have designed our comprehensive PLC programs to deliver process consistency from the time customer parts are loaded into one of our plating lines until they come out meeting all quality requirements. As a job shop, we plate thousands of different parts for hundreds of different customers across a wide range of industries. It is our tightly controlled process and system integration - from the time customer parts are received on our dock until they are shipped back out - that allows us to consistently deliver results that meet or exceed our customers’ expectations.
Technology Beyond Automated Plating Lines
While PLCs and automated plating lines may grab the headlines, Varland employs many other technological systems in our never-ending pursuit of continuous improvement. We never want to rest on our laurels so we’re constantly looking for ways to innovate. Check out some of the other ways we leverage technology in our plant:
Centralized database of x-ray plating thickness results aggregating data from multiple x-ray machines for historical analysis of thickness and alloy percentage trends
Continuous recording of screenshots on plant computers running HMI software allowing for management review and troubleshooting
Custom project management application designed as part of our quality management system for tracking corrective actions and continuous improvement projects
Data historian with built in redundancy allowing tracking, analysis, and visualization of metrics from PLCs and other systems
Custom API that allows our PLC programs to flag plating exceptions requiring quality control personnel to review orders before final approval
Fully automated waste water system ensuring compliance with local regulations and upholding company commitment to environmental stewardship
PLC monitoring and control of ovens (traditional and inert atmosphere) used for baking to relieve hydrogen embrittlement and for hardness
Centralized databases and applications for tracking salt spray performance, hardness tests, calibrations, plating specifications, preventive maintenance, and more
Varland’s Organizational Commitment to Technological Excellence
The extent that Varland leverages technology requires an extraordinary commitment. Innovative technology requires vision and creativity, and team members from all levels of the organization have always been encouraged to bring their ideas forward. Through the years, many employee ideas have been implemented.
We’re not the largest plating company but we feel we’re one of the best. One of the challenges of achieving technological excellence for a company of our size is navigating a marketplace that caters mainly to large teams and even larger budgets. It is also a challenge to integrate different systems (from multiple vendors) that were never intended to work together. Without Varland’s embrace of technology at all levels of the organization for decades, the results we have delivered simply would not have been possible.
Whether that commitment manifests itself in deploying a group of open source applications rather than proprietary software or writing a custom translation layer to get historical PLC data into our data historian, we will continue to seek new ways to leverage technology for the benefit of our customers.
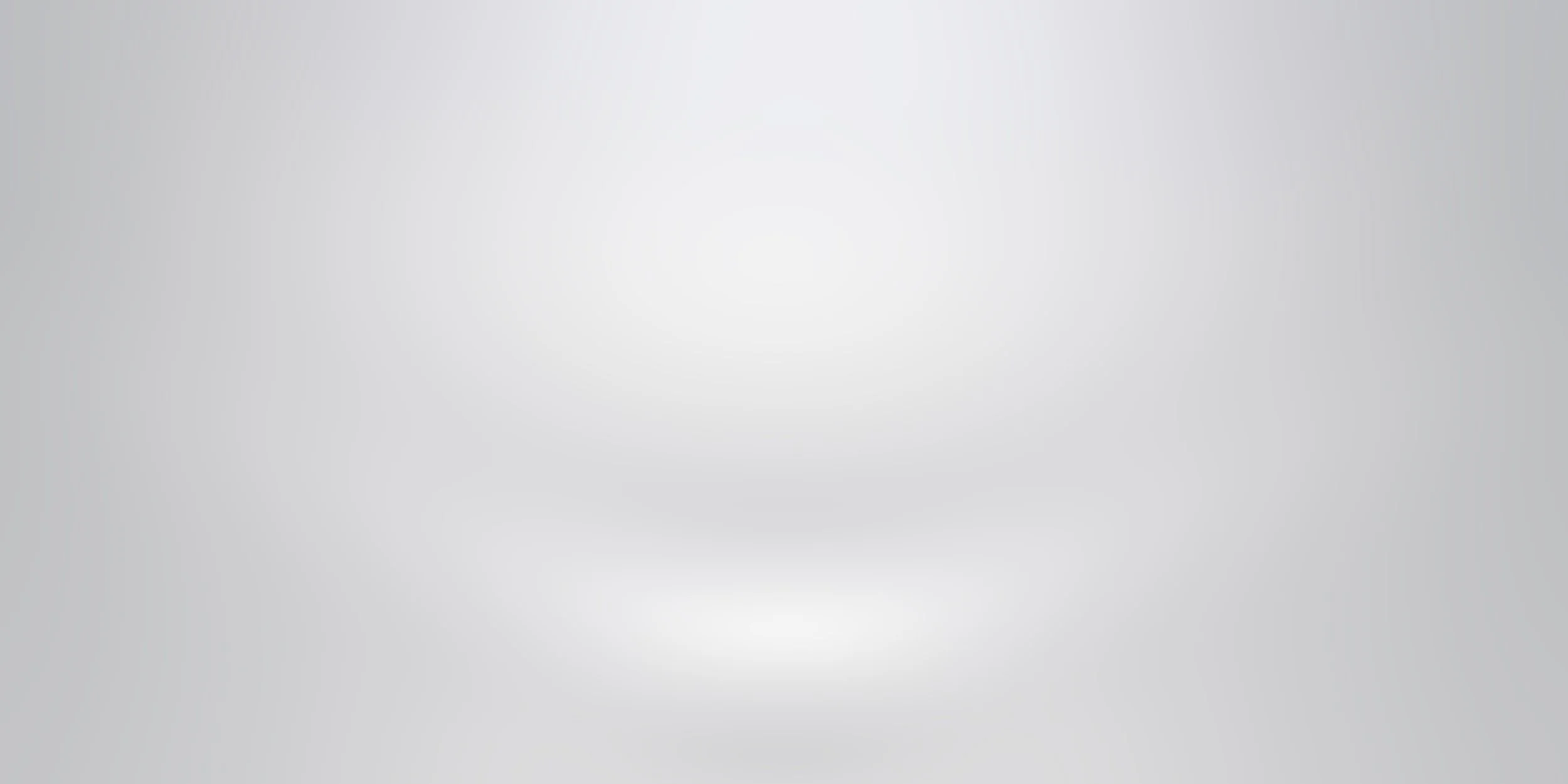
In addition to delivering industry-leading plating quality, Varland Plating always strives to offer our customers great customer service. We know there’s nothing more frustrating than automated phone systems, constant voicemails, phone tag, or waiting for responses to emails. We work extremely hard to be responsive and easy to reach, and our new customer portal is an extension of our goal to make things easy for our customers.
Our portal, available to all customers free of charge, allows easy access to near-realtime status information about all jobs at Varland and all shipments made by Varland in the last 30 days.
For jobs at Varland, you’ll see all the relevant information about your jobs, including our order number, part number, your purchase order number(s), and part quantities. You’ll also see the status of your order, color coded to make it easy to understand at a glance.
For jobs that have shipped, you’ll have access to even more helpful information. You’ll be able to download PDF copies of certifications for orders that include certifications and PDF copies of Varland’s packing list for all shipments. You’ll see the shipping method and tracking information, including links directly to carrier tracking whenever possible.
All of this is designed to make things easier and faster for you. Whether you need a copy of a recent certification, proof of delivery from a trucking company, or an inventory of all your jobs at Varland, now you can have access to that information any time and from any device.
Portal Features We Know You’re Going To Love:
For carriers that support it, we provide links to tracking websites. This makes it very easy to learn exactly where your parts are when they’re en route and to obtain proof of delivery when it’s required.
We make it easy for you to get electronic copies of plating certifications. We’ve always been happy to email certifications on request, but now you can get PDF copies without needing us to email them or having to scan them.
Our portal features a responsive design. Whether you’re on a desktop, laptop, or mobile device, all your information is at your fingertips.
We prioritized speed and a clean design, so there is no clutter and nothing to prevent you from finding what you need quickly.